Handbook Of Garments Manufacturing Technology
Posted : admin On 07.02.2020- Garment Manufacturing Industry
- Handbook Of Garments Manufacturing Technology Inc
- Handbook Of Garments Manufacturing Technology Jobs
Fig: Common abbreviations for textiles and garments technology Important Abbreviations for Textile and Apparel Manufacturing Technology: 1. BGMEA:Bangladesh Manufacturers and Exporters Association 2. BKMEA:Bangladesh Knitwear Manufacturers & Exporters Association 3. BTMC:Bangladesh Textile Mills Corporation 4. BTMA:Bangladesh Textile Mills Association 5. BGWUC:Bangladesh Garments Unit Council 6.
WTO:World Trade Organization 7. AQL:Acceptable Level 8. CBL:Center Back Line 9. CFL:Center Front Line 10. FOB:Free On Board 11. GPT:Garments Performance 12.
EPB:Exporter Promotion Bureau 13. C & F:& Freight 14. CIF:Cost, Insurance and 15. CMO:Order 16. CMT:Cost of Making with 17. NSA:No Allowance 18. BL:Bill of Loading 19.
CO:Certificate of Origin 20. BB L/C:Back to Back L/C 22.
UD:Utilization Declaration. AAQC:American Association of 24. LCA:Letter of Credit Authorization 25. PSI:Pre-Shipment 26.
Garment Manufacturing Industry
M and W:Men and Women 27. W and G:Women and Girl 28. XL:Extra Large (Size) 29. L:Large (Size) 30.
M:Medium (Size) 31. S:Small (Size) 32.
CAD:Computer Aided Design 33. CAM:Computer Aided Manufacturing 34. PTS:Primary Textile Sector 35. GDP:Growth Domestic Product 36. ISO:International Organization for Standardization 37. GSP:Generalized System of Preferences 38.
GATT:Generalized Agreement on Tariffs and Taxes 39. MFA:Multi Fiber Arrangement 40. EPB:Promotion Bureau 41.
FY:Financial Year 42. PTI:Private Textile Industry 43. VAT:Value Added Tax 44.
P/C:Polyester + 46. T/C:Tetron + Cotton 47. MOT:Ministry of Textile 48.
MOC:Ministry of Commerce 49. CNF:Clearing & Forwarding 50. BWTG:Better Worker in Textile Garments 51. EPI:Ends per Inch 52. PPI:Picks per Inch 53. ILO:International Labor Organization 54.
IMF:International Monetary Fund 55. IFTU:International Federation of Trade Union 56. PO:Production Officer 57. PM:Production Manager 58. AGM:Assistant General Manager 59. GM:General Manager 60. CEO:Chief Executive OfficerYou may also read the below articles:Facebook Comments.
× VitalSource eBookVitalSource Bookshelf gives you access to content when, where, and how you want.When you read an eBook on VitalSource Bookshelf, enjoy such features as:. Access online or offline, on mobile or desktop devices. Bookmarks, highlights and notes sync across all your devices. Smart study tools such as note sharing and subscription, review mode, and Microsoft OneNote integration.
Search and navigate content across your entire Bookshelf library. Interactive notebook and read-aloud functionality.
Look up additional information online by highlighting a word or phrase. The Textile Institute and Woodhead Publishing.
List of contributors. Woodhead Publishing Series in Textiles.
1. Introduction: the apparel industry. 1.1. Introduction. 1.2. Global scenario of apparel manufacturing.
1.3. Challenges in apparel production. 1.4. Role of various organisations. 1.5. Future trends. 1.6.
Conclusions. Part One. Product development, production planning and selection of materials. 2. Product development in the apparel industry. 2.1. Introduction.
2.2. Product-development models and product-development process. 2.3. Variations in apparel product development: demand-led product development.
2.4. Apparel product-development technologies. 2.5. Apparel product standards, specifications, quality assurance and product technical package. 2.6.
Apparel product life-cycle management (PLM) and supply-chain relationships. 2.7. Measures for apparel product development. 2.8. Future trends in apparel product development. 2.9.
Case studies: PD tools and technologies. 2.10. Conclusions. 2.11. Sources of further information and advice. 3.
Role of fabric properties in the clothing-manufacturing process. 3.1. Introduction. 3.2. Fabric properties and performance. 3.3. Garment make-up process and fabric properties.
3.4. Low-stress mechanical properties and make-up process.
3.5. Control system. 3.6.
Fabric tailorability, buckling and formability. 3.7. Sewability. 3.8. Conclusions. 4. Production planning in the apparel industry.
4.1. Introduction. 4.2. Production planning. 4.3. Production systems. 4.4.
Production planning and control in the apparel industry. 4.5.
Supply chain management in the apparel industry. 4.6. Inventory management. 4.7.
Manufacturing performance improvement through lean production. 4.8. Waste management.
4.9. Human resource management.
4.10. New tools developed in production planning. 5. Fabric sourcing and selection. 5.1. Introduction. 5.2.
Fabric sourcing. 5.3.
Fabric inspection. 5.4. Future trends. 5.5. Conclusions.
6. Selecting garment accessories, trims, and closures. 6.1. Part 1: introduction to garment accessories.
6.2. Part 2: selecting garment accessories. 6.3. Part 3: selecting supporting materials.
6.4. Part 4: selecting closures. 6.5. Part 5: accessories for children's wear.
6.6. Part 6: evaluation of quality of trims and accessories. 6.7.
Part 7: fashion accessories. 6.8. Conclusions. Part Two. Garment design and production. 7.
Garment sizing and fit. 7.1. Introduction. 7.2. Geometry of the human form.
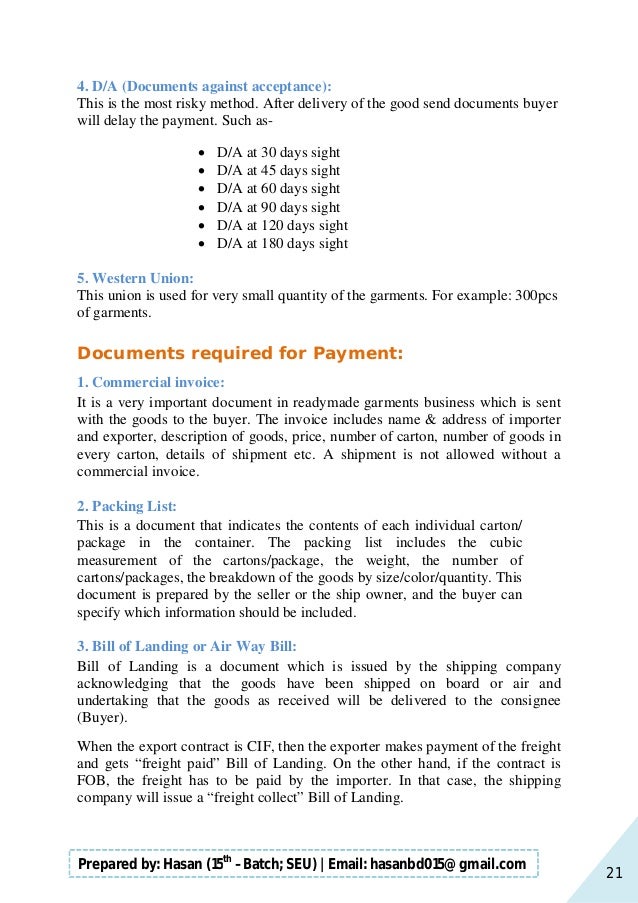
7.3. The human figure divided into body proportions. 7.4. Garment size charts.
7.5. Development of garment size charts. 7.6. Sizing and fit systems.
7.7. Three-dimensional (3D) body scanning – current and potential future applications in clothing manufacture and retailing. 7.8. Conclusions.
7.9. Sources of further information. 8. Pattern construction. 8.1. Introduction.
8.2. Pattern construction modes. 8.3. Body, material and design. 8.4. Pattern construction tools.
8.5. Conclusions. 8.6. 2D and 3D CAD Web sites. 9.
Fabric spreading and cutting. 9.1. Introduction. 9.2.
Cut process planning. 9.3. Spreading of textile materials. 9.4. Cutting of textile materials. 9.5. Fusing of cut textile components.
9.6. Final work operations of the cutting process. 9.7. Future trends. 9.8.
Conclusions. 10. Sewing, stitches and seams. 10.1. Introduction. 10.2. Stitch classes.
10.3. Seam types. 10.4.
Seam-neatening. 10.5. Future trends. 10.6. Conclusions. 10.7.
Sources of further information and advice. 11. Sewing equipment and work aids.
11.1. Introduction. 11.2.
Different bed types in industrial sewing machines. 11.3.
Different feed types in industrial sewing machines. 11.4. Cyclic sewing machines. 11.5.
Computerised sewing machines. 11.6. Work aids. 11.7.
Sewing automats. 11.8. Sewing needles.
11.9. Sewing threads. 11.10. Future trends and conclusions. 11.11. Sources of further information and advice. 12.
Sewing-room problems and solutions. 12.1. Introduction. 12.2. Seam pucker and other surface distortions. 12.3.
Sewing defects caused by needles. 12.4. Material feeding and associated problems.
12.5. Problems in stitch formation. 12.6.
Thread breakage. 12.7. Future trends. 12.8. Conclusions. 12.9. Sources of further information and advice.
13. Alternative fabric-joining technologies. 13.1. Alternatives to sewing.
13.2. Adhesive bonding. 13.3. Conventional thermal welding. 13.4. Advanced thermal-welding processes. 13.5.
Conclusions. 14. Seamless garments. 14.1. Introduction.
14.2. Seamless technique. 14.3. Common seamless products.
14.4. Raw materials. 14.5. Seamless knitting machines. 14.6.
Advantages of seamless garments. 14.7. Disadvantages of seamless garments. 14.8. Applications of seamless garments. 14.9.
Future developments. 14.10. Conclusions. Part Three. Garment finishing, quality control, care labelling and costing. 15.
Garment-finishing techniques. 15.1. Introduction. 15.2.
Garment finishing for functionality. 15.3. Knitwear finishing. 15.4. Denim garment finishing. 15.5.
Pressing (factors and equipment). 15.6.
Future trends. 15.7. Conclusions. 16. Quality control and quality assurance in the apparel industry. 16.1. Introduction.
16.2. Quality control in the apparel industry.
16.3. Future trends. 16.4. Conclusions.
16.5. Sources of further information and advice. 17. Care labelling of clothing.
17.1. Introduction. 17.2.
Requirements of care labelling. 17.3. Definition of care label. 17.4.
Care labelling systems. 17.5. Future trends. 17.6. Conclusions. 18.
Handbook Of Garments Manufacturing Technology Inc
Garment costing. 18.1. Introduction. 18.2.
Costing need. 18.3.
Handbook Of Garments Manufacturing Technology Jobs
Cost classification. 18.4. Cost elements. 18.5. Measures of efficiency.
18.6. Profitability. 18.7. Garment sales element analysis.
18.8. Mark-downs.
18.9. Managing cost through inventory control. 18.10. Apparel costing sheet analysis.
18.11. Conclusions. Index. Garment Manufacturing Technology provides an insiders' look at this multifaceted process, systematically going from design and production to finishing and quality control.As technological improvements are transforming all aspects of garment manufacturing allowing manufacturers to meet the growing demand for greater productivity and flexibility, the text discusses necessary information on product development, production planning, and material selection. Subsequent chapters covers garment design, including computer-aided design (CAD), advances in spreading, cutting and sewing, and new technologies, including alternative joining techniques and seamless garment construction.
Garment finishing, quality control, and care-labelling are also presented and explored. Key Features. Rajkishore Nayak is currently working as a senior lecturer (Fashion Merchandising) at the Centre of Communication and Design, RMIT University, Vietnam. He completed his PhD from the School of Fashion and Textiles, RMIT University, Australia. He has around 15 years of experience in teaching and research related to Fashion and Textiles. He published about 90 peer-reviewed papers in national and international journals.
Recently, Rajkishore was awarded with the 'RMIT University Research Excellence Award-2015'. He also received the 'RMIT University Teaching and Research Excellence Award-2012' and 'RMIT University International Scholarship-2008'. He worked with the School of Fashion and Textiles, RMIT University, Australia from 2012-2016 in teaching and research. Professor Rajiv Padhye is a Director of a Centre for Materials Innovation and Future Fashion at the School of Fashion and Textiles, RMIT University, Australia.
He did his PhD from Leeds University, UK. He has several national and international publications in various journals.
Rajiv has supervised many PhD and Masters Students and published several book chapters, monogram, journal articles and books. Recently Rajiv has been honored by RMIT University with “Research Leadership” 'Research excellence'and “Media Person 2012” awards. In 2003 Textile Institute, Manchester UK, has honoured him with Fellowship of the Textile Institute (FTI).